Custom watch build #2: “Glass – Parallel”
Note: This was not an exercise in design, but rather an exercise in process.
![]() |
![]() |
Glass – 42 | Glass – Parallel |
The details:
- Brand & Model: 10/6 Glass – Parallel
- Diameter: 42mm
- Height: 11.1mm
- Movement: Chinese F8131, modified hand-wound
- Power Reserve: 40 hours
- Jewels: 17
- Lume: N/A
- Frequency: 21,600bph (3Hz)
- Crystal: Mineral, Flat
- Water Resistance: 100m/300ft
- Strap: Torro Brava Italian Leather, Black
When I first started tinkering with putting my own watches together, I quickly realized that getting all the components was an issue and then getting all the components to play nicely together was another issue. The primary obstacle I have encountered is the movement holder/ring.
The movement ring is the interface between the movement and the rest of the watch. As I mentioned in [Glass], the key is the holder. After some time and energy exploring different avenues, I have learned that the chances of finding a movement ring that is the right fit between a randomly chosen movement and a particular case are slim to none. Cases and holders are designed and ordered for mass production runs in China, given a particular movement.
For my first watch build, I chose a case that came with a movement holder for common Sellita movements (200, 210, 220). But, that is not what I had initially planned. I wanted to try a cheaper watch movement in a nice case. Specifically, a Chinese F8131 movement in a 42mm stainless steel case from Ofrei.com. Why that movement? It looks ok, tells time, and is $100 less than a Swiss movement.
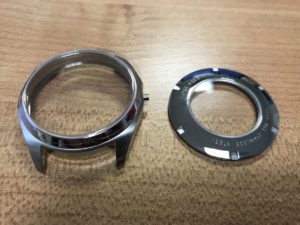
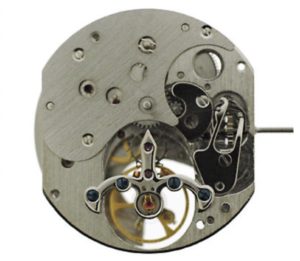
As a computer scientist with some technical know-how and access to some useful technology an idea struck me: 3d-printing. Why not take some measurements, draft a modified movement holder with AutoCAD and/or SolidWorks, and print it!
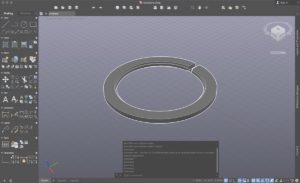
To alleviate any suspense, it worked. But it did take several attempts to get the dimensions (tolerances) and process figured out. For example, should the holder be printed top-to-bottom or bottom-to-top, that decision impacts quality. (I found was top-to-bottom was best.) Also, trying different colors, ring thickness, etc. A positive attribute of 3d-printing is the cost. For me the cost is free, but if I were to pay it would be about $0.15 per print. For reference I was printing with an Ultimaker3. And white seemed to work better than black.
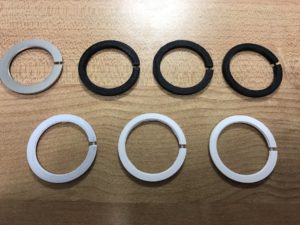
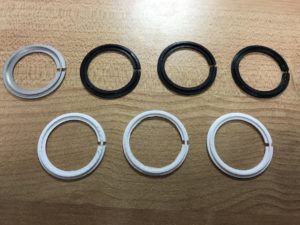
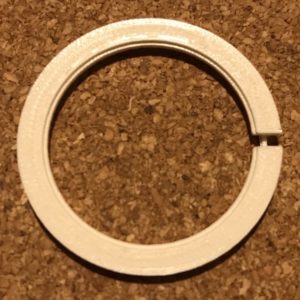
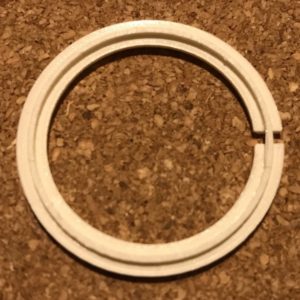
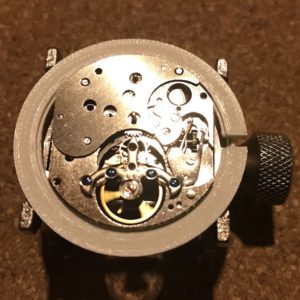
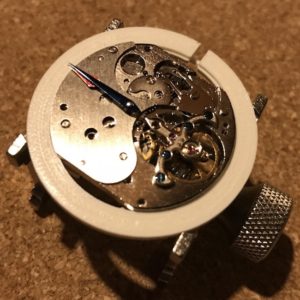
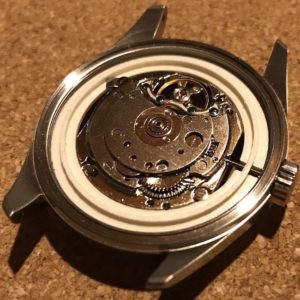
Note the casing screws @ 4 and 10

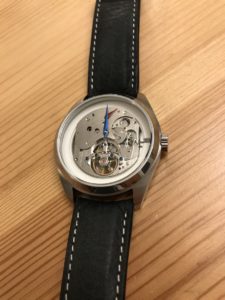
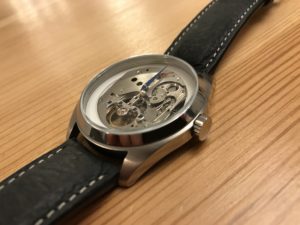
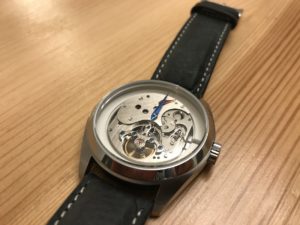
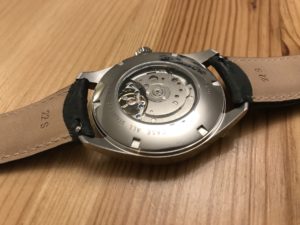
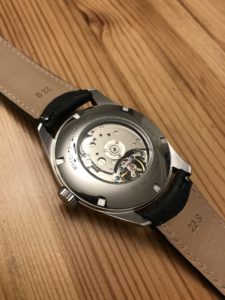
Fantastic. I’d like to put a Felsa 690 inside a Chinese case and you have lit my way. Thanks very much. Now I have to decide to buy the right and economic 3D printer. Is PLA a good material to do this work? Thanks
I use PLA for making my movement holders, which works fine, but you will need a decent 3D printer. A $200 put it together yourself printer probably won’t get you the results you want. If you want to get into 3D printing or will do this sort of thing regularly then get a good printer. If it’s just a one-off print, then find someone with a good printer to print it for you.